How to Select a Pigging System for Maximum Product Recovery and Process Efficiency
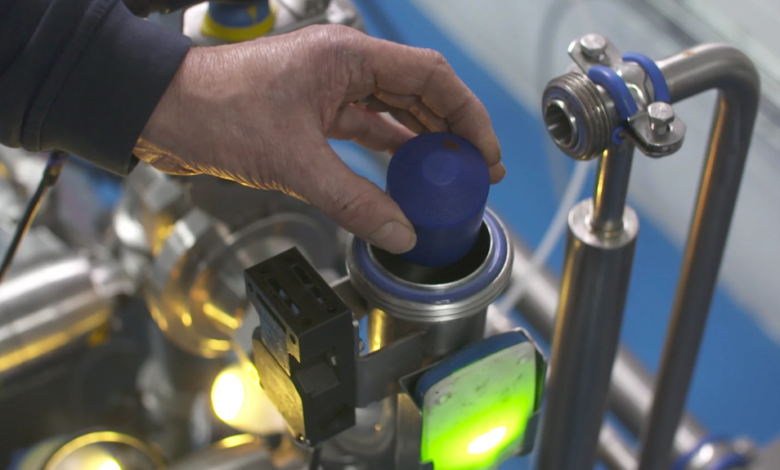
In today’s competitive industrial environment, the need for efficient production systems that minimize waste and maximize output is more critical than ever. One such solution that delivers on both fronts is a pipeline pigging system. But knowing how to select a pigging system that matches your company’s operations is where the real strategy lies.
Pigging systems are widely used in industries like food and beverage, cosmetics, paints, personal care, chemicals, and pharmaceuticals. These systems use a specially designed projectile, known as a pig, to clear out product remaining in pipelines, separating batches or aiding in pipeline cleaning. While their use is widespread, not all pigging systems are created equal. This article provides a complete guide on how to select a pigging system that meets your unique operational and commercial needs.
What Is Pigging?
Before you begin the selection process, it’s important to understand what a pigging system does. At its core, a pigging system uses a pig—a solid, cylindrical, or flexible object that fits snugly within a pipeline—to push out residual product, separate different batches, or clean the interior surfaces of the pipeline.
Modern pigging systems are often automated and integrated into production processes to improve efficiency, save resources, and ensure product purity. With the right system, you can recover product that would otherwise go to waste, reduce cleaning time, and lower water and chemical usage.
See also: A Complete Guide to the icp aes instrument: Technology, Applications, and Benefits
Why Selecting the Right System Matters
To select a pigging system effectively, you must consider more than just initial costs. A mismatched or poorly designed system can result in:
- Insufficient product recovery
- Downtime and maintenance issues
- Pigging failures due to pipeline design incompatibility
- Hygiene risks in sensitive production environments
- Increased operational costs
In contrast, a well-chosen system delivers measurable ROI through faster changeovers, improved product yield, and better sustainability metrics.
Step 1: Define Your Product and Process Parameters
The first step to select a pigging system is understanding the properties of your product:
- Viscosity: Thicker products like peanut butter, lotion, or paint require pigs that can exert more pressure and maintain a strong seal.
- Chemical Composition: Highly acidic, alkaline, or abrasive substances may require chemically resistant materials for both the pig and the pipeline.
- Product Value: High-value products make pigging more economically attractive due to greater potential for product recovery.
Also consider your process frequency:
- How often do you change batches?
- How much residual product is typically lost per run?
- Are your processes continuous or batch-based?
Understanding these inputs helps tailor a system that fits both the product and your production cycle.
Step 2: Analyze Pipeline Design and Layout
No pigging system will function optimally unless it fits seamlessly into your existing pipeline design. Carefully assess:
- Pipeline diameter: Determines the pig’s size and design.
- Length of pipeline: Affects the required propulsion force and system complexity.
- Bends and elbows: Some pigs navigate curves better than others.
- Vertical or horizontal orientation: May require different propulsion methods (e.g., compressed air, CO₂, or product push).
- Multiple branches: If pipelines are interconnected, you may need a multi-line pigging system or diverter valves.
Taking these physical attributes into account ensures the system you choose is practical and fully functional.
Step 3: Choose Between Manual, Semi-Automated, and Fully Automated Systems
When you select a pigging system, think about the level of automation your operation requires:
- Manual systems: Cheaper upfront, but require human intervention and are suited for low-volume or infrequent production.
- Semi-automated systems: Strike a balance between automation and manual control, using some sensors or control panels to trigger the pigging process.
- Fully automated systems: Ideal for high-volume, multi-product facilities. These systems are integrated into the production line and controlled via PLC (Programmable Logic Controller) or SCADA software.
Automated systems improve speed, consistency, and safety—but they also come with a higher investment cost.
Step 4: Select the Right Pig Type
When you select a pigging system, the pig itself must be chosen wisely. Consider:
- Solid pigs: Highly durable and ideal for straight pipelines.
- Foam pigs: Flexible, lightweight, and better for pipelines with multiple bends.
- Sanitary pigs: Made with FDA-approved materials for use in food, beverage, and pharmaceutical settings.
- Smart pigs: Equipped with sensors and used primarily in oil and gas pipelines for detecting pipeline integrity issues.
Pigs should be compatible with your product, easily cleaned, and long-lasting to ensure the system remains cost-effective over time.
Step 5: Ensure Regulatory Compliance and Cleanability
In regulated industries like pharma or food processing, hygiene and traceability are critical. To maintain compliance:
- Choose sanitary pigging systems with hygienic design principles (smooth surfaces, no dead legs, easy to disassemble and clean).
- Use materials approved by FDA, EHEDG, or other industry standards.
- Integrate cleaning-in-place (CIP) or sterilization-in-place (SIP) where necessary.
When you select a pigging system, overlooking compliance can result in failed audits or even product recalls.
Step 6: Consider Maintenance and Downtime
Even the best pigging systems require occasional servicing. Make sure the system you select:
- Has easily accessible parts
- Offers long-lasting components
- Includes training for your team
- Is backed by strong technical support
Downtime is costly. A system that’s reliable and easy to maintain will protect your investment and ensure smooth operations.
Step 7: Evaluate Cost vs. Long-Term Return
While cost is often the deciding factor, remember that cheap systems can become expensive if they underperform or require frequent repairs.
Calculate the total cost of ownership, including:
- Initial investment
- Installation and commissioning
- Spare parts and maintenance
- Downtime from inefficient systems
Then weigh that against the benefits:
- Annual product recovery savings
- Reduced cleaning costs
- Faster changeovers
- Environmental and regulatory compliance
The goal is to select a pigging system that pays for itself quickly and continues to deliver returns for years.
Conclusion
To successfully select a pigging system, you must align your decision with your product properties, pipeline design, process goals, compliance requirements, and budget. The right system should improve your operational efficiency, product recovery, and sustainability efforts—delivering a rapid and reliable return on investment.
By planning carefully and working with the right solution provider, you can implement a pigging system that not only meets today’s requirements but is scalable and adaptable for future production challenges.